砂光机调整、常见故障及砂光板缺陷分析
砂光机调整、常见故障及砂光板缺陷分析
砂光在人造板生产中至关重要,运用磨削量分配原则精细调整砂光机,及时处理砂光机常见故障,正确分析砂光板存在缺陷,才能使砂光机正常运行又砂削出合格的坯。
掌握砂光机调整方法,及时处理砂光机常见故障,正确分析砂光板顾在缺陷,才能使砂光机既正常运行又砂削合格的板坯。
1、砂光机的调整
1.1磨削量分配
由于人造板生产厂规模不断扩大,目前砂光线大多采用2台或3台砂光机组合的形式,即“2+4”、“4+4”或“2+4+4”组合,砂光分成3道,4道,5道。采用这种多道磨削的组合形式就必须正确分配各道砂光的磨削量。
1)磨削量分配前提正确分配磨削量,首先应确定下列前提:
①磨削总量。
②砂光机砂光道数。
③砂带粒度分配,特别是最后一道的砂带粒度。
2)磨削量分配原则
①充分利用粗、精、细砂带特点,适量分配磨削量,一般精磨、细磨的磨削量可以预先确定下来,粗砂视实际情况而定;
②精砂量、细砂量不能太小,必须能去除上一道砂痕。
③在达到最佳磨削表面的同时使电能,砂带消耗最少。
3)磨削量分配 磨削量分配一般采用倒推法。先确定最后一道磨削量,再确定最后第二道磨削量,最后确定第一道磨削量。
例:某公司采用“4+4”砂光组合,根据市场对板面质量要求,最后一道要求采用150#砂带,总磨削量为2.2~2.8mm。根据上述条件,首先选择砂带为40#、80#、120#、150#,再选择第五道磨削量为0.15mm(双面,组合砂架的磨垫),第三道磨削量为0.5mm。余下的1~1.6mm为第一道磨削量。
4)磨削量分配的操作 采用逐道操作的方法,首先根据分配的磨削量,确定每道砂光完成以后的板厚尺寸。根据确定的板厚尺寸,先砂第一道,后几道砂带时去掉。第一道砂光板厚尺寸满足要求后,套上第一道砂带进行磨削,确定第二道板厚尺寸。以此类推,直到最后一道尺寸符合要求。一般在确定每道尺寸时,至少砂两张板符合尺寸要求,方能确定这道砂光已调整正确。0.15mm 0.15mm 0.4mm 0.5mm 1~1.6mm 5)磨削量分配不当引发的问题:
①粗砂磨削量太小,会增加精砂、细砂的负担,使精、细砂带消耗量增加,同时不能充分利用粗砂功能,送进速度有所下降,影响生产效率。
②前道磨削量太多或后道磨削量太少,都会引起密集模向波纹(实际是前道横向波纹未消除,后道又同时产生,两道横向波纹重叠),表面光洁度降低。
可见,正确分配磨削量,不仅可以提高板面质量,而且可以节省砂带,降低能耗,提高生产效率。
值得注意的是采用上述办法调整完毕后,应根据实际情况在使用过程中做适当微量调整,因为磨削过程是不变数:砂带磨损,磨垫磨损,板的密度和硬度在变化。如何进行微调,需要不断积累经验,摸透每一台设备的机械特性。
按上述方法调整完毕后,以后一般不需要做大的调整,即使在变换板坯的规格时也不需要做大的调整,但为此应对偏心轮、磨垫位置作记录,避免有人误操作而造成需要重新调整。
为实现砂光机磨削量正确分配,就必须对砂光机进行调整。砂光机调整一般采用下机架基准原则,即首先调整下机架,然后以下机架为基准调整上机架。调整下机架比较困难,必须升起上机架,采用平尺及条式水平仪精细调整,耗时较长。因此用户调整完下机架后,应保持下机架状态,做好必要的记号,这样会大大节省时间。通常机器出厂前,已基本调整完毕,调试人员在现场微调即可,但用户使用一段时间或更换主要另部件时,会作大范围调整。
延伸阅读:砂光机保养方法?
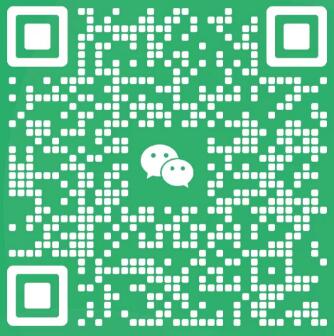
添加中木商网客服微信咨询
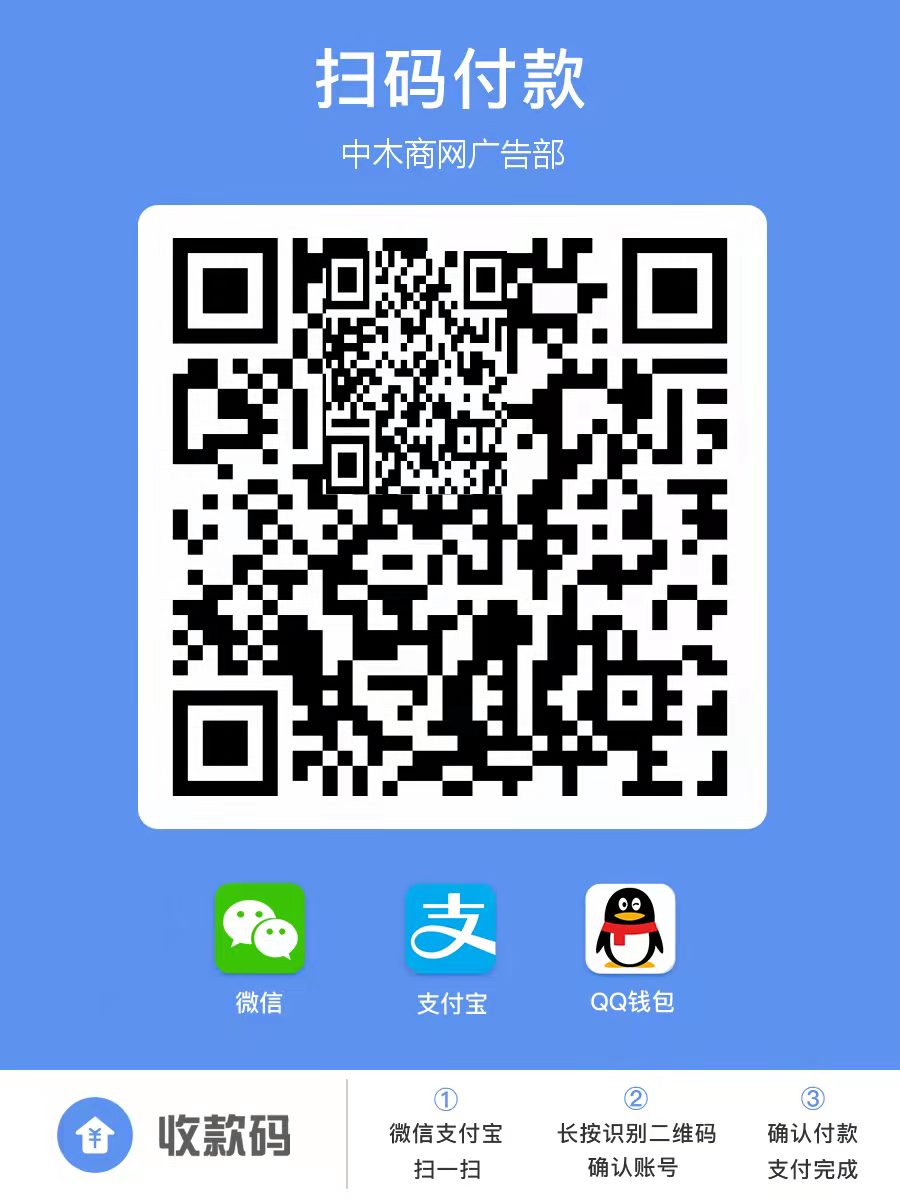
中木商网推广付款微信二维码
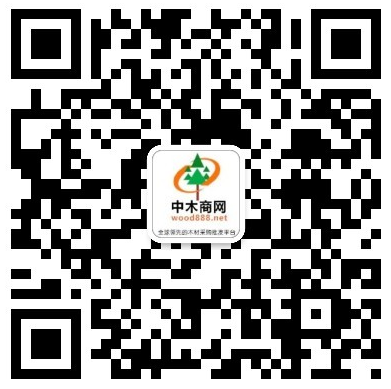
会员绑定中木商网微信公众号